1. What is the role of each element in the diamond saw blade matrix binder?
The role of copper: Copper and copper based alloys are the most commonly used metals in metal binder diamond tools, with electrolytic copper powder being the most commonly used. Copper and copper based alloys are so widely used because copper based binders have satisfactory comprehensive properties: lower sintering temperature, good formability and sinterability, and miscibility with other elements. Although copper hardly wets diamonds, certain elements and copper alloys can significantly improve their wettability towards diamonds. One of the elements such as Cr, Ti, W, V, Fe that form copper and carbides can be used to make copper alloys, which can greatly reduce the wetting angle of copper alloys on diamonds. The solubility of copper in iron is not high. If there is excessive copper in iron, it sharply reduces the heat workability and causes material cracking. Copper can form various solid solutions with nickel, cobalt, manganese, tin, and zinc, strengthening the matrix metal.
The function of tin: Tin is an element that reduces the surface tension of liquid alloys and has the effect of reducing the wetting angle of liquid alloys on diamonds. It is an element that improves the wetting of bonded metals on diamonds, reduces the melting point of alloys, and improves the formability of pressing. So Sn is widely used in adhesives, but its use is limited due to its large expansion coefficient.
The role of zinc: In diamond tools, Zn and Sn have many similarities, such as low melting point and good deformability, while Zn is not as good at changing the wettability of diamond as Sn. The vapor pressure of metal Zn is very high and it is easy to gasify, so it is important to pay attention to the amount of Zn used in diamond tool binders.
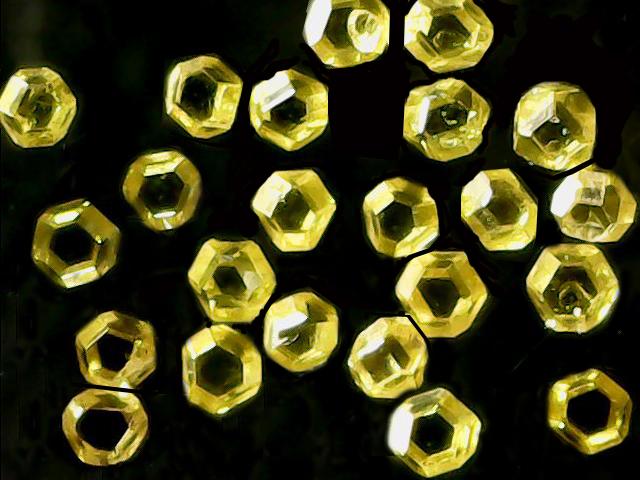
The role of aluminum: Metal aluminum is an excellent light metal and a good deoxidizer. At 800 ℃, the wetting angle of Al on diamond is 75 °, and at 1000 ℃, the wetting angle is 10 °. Adding aluminum powder to the binder of diamond tools can form carbide phase Ti Å AlC and intermetallic compound TiAl in the matrix alloy.
The role of iron: Iron has a dual role in the binder, one is to form carburized carbides with diamonds, and the other is to alloy with other elements to strengthen the matrix. The wettability of iron and diamond is better than that of copper and aluminum, and the adhesion work between iron and diamond is higher than that of cobalt. When an appropriate amount of carbon is dissolved in Fe based alloys, it will be beneficial for their bonding with diamonds. Moderate etching of diamonds by Fe based alloys can increase the bonding force between the bond and diamond. The fracture surface is not smooth and bare, but covered by a layer of alloy, which is a sign of enhanced bonding force.
The role of cobalt: Co and Fe belong to the transition group elements, and many characteristics are similar. Co can form carbide Co ₂ C with diamond under specific conditions, while also spreading an extremely thin cobalt film on the surface of diamond. In this way, Co can reduce the internal interfacial tension between Co and diamond, and has significant adhesion work to diamond in the liquid phase, making it an excellent bonding material.
The role of nickel: In the binder of diamond tools, Ni is an indispensable element. In Cu based alloys, the addition of Ni can infinitely dissolve with Cu, strengthen matrix alloying, suppress low melting point metal loss, and increase toughness and wear resistance. Adding Ni and Cu to Fe alloys can lower the sintering temperature and reduce the thermal corrosion of bonded metals on diamonds. Choosing an appropriate combination of Fe and Ni can greatly improve the holding power of Fe based binders on diamonds.
The role of manganese: In metal binders, manganese has a similar effect to iron, but has strong permeability and deoxygenation ability, and is prone to oxidation. The addition amount of Mn is generally not high, and the main consideration is to use Mn for deoxidation during sintering alloying. The remaining Mn can participate in alloying and strengthen the matrix.
The role of chromium: Metal chromium is a strong carbide-forming element and also a widely used element. In the diamond groove saw blade matrix, there is sufficient chromium to have a sound attenuation effect, which is related to the activation energy of Cr. Adding a small amount of Cr to the Cu based matrix can reduce the wetting angle of the copper based alloy to diamond and improve the bonding strength of the copper based alloy to diamond.
The role of titanium: Titanium is a strong carbide forming element that is easy to oxidize and difficult to reduce. In the presence of oxygen, Ti preferentially generates TiO2 instead of TiC. Titanium metal is a good structural material with strong strength, less strength reduction at high temperatures, heat resistance, corrosion resistance, and high melting point. Research has shown that adding an appropriate amount of titanium to the diamond saw blade matrix is beneficial for improving the service life of the saw blade.
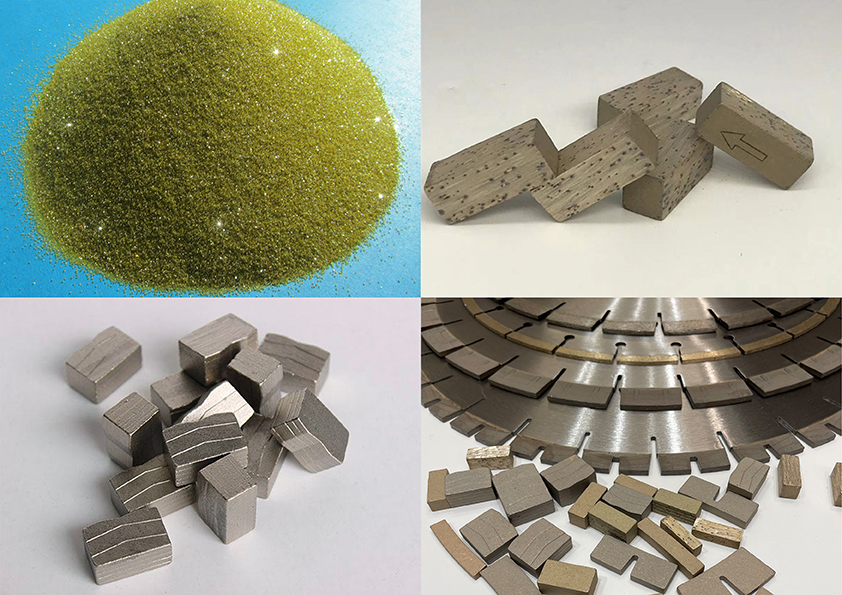
2. Why should the saw blade body match the cutting stone?
The main methods of rock fragmentation during the saw blade cutting process are fracturing and crushing, as well as large volume shear and fragmentation, supplemented by surface grinding. A diamond with a serrated working surface that serves as a cutting tool. Its cutting edge is the extrusion area, the cutting area is in front of the edge, and the grinding area is on the back edge. Under high-speed cutting, diamond particles work on the support of the matrix. During the process of cutting stone, on the one hand, diamond undergoes graphitization, fragmentation, and detachment due to high temperature generated by friction; On the other hand, the matrix is worn by the friction and erosion of rocks and rock powder. Therefore, the issue of adaptability between saw blades and rocks is actually the issue of wear rate between diamond and matrix. The characteristic of a tool that works normally is that the loss of diamond matches the wear of the matrix, keeping the diamond in a normal state of cutting edge, neither premature detachment nor smooth and slippery diamond grinding, ensuring that its grinding effect is fully utilized during operation, resulting in more diamonds being in a slightly fractured and worn state. If the strength and impact resistance of the selected diamond are too low, it will lead to the phenomenon of "shaving", and the tool's lifespan will be low and the passivation will be severe, and even the sawing will not move; If excessively high strength abrasive particles are selected, the cutting edge of the abrasive particles will appear in a flattened state, resulting in an increase in cutting force and a decrease in processing efficiency.
(1) When the wear speed of the matrix is greater than that of the diamond, it leads to excessive diamond cutting and premature detachment. The wear resistance of the saw blade body is too low, and the saw blade life is short.
(2) When the wear speed of the matrix is less than that of the diamond, the new diamond is not easily exposed after the diamond cutting edge is worn, the serrations have no cutting edge or the cutting edge is very low, the surface of the serrations is passivated, the cutting speed is slow, and it is easy to cause the cut board to fall off, affecting the processing quality.
(3) When the wear speed of the matrix is equal to the wear speed of the diamond, it reflects the compatibility of the matrix with the cut stone.
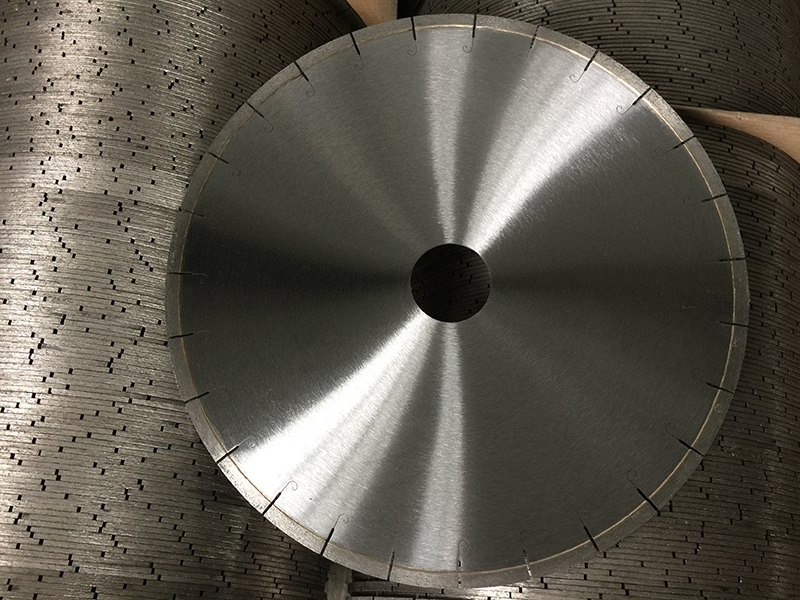
Post time: Aug-11-2023